Modern work culture traces its roots to late 18th-century English factories, where pioneering assembly lines and labor division transformed economic centers and social structures.
Discover how Henry Ford's innovations and technological advances reshaped work practices, driving mass production and urbanization worldwide.
Origins of the Factory System
The factory system's origins in late 18th-century England revolutionized production by centralizing work processes and introducing mechanization. You can trace this significant shift to the textile mills, where the assembly line concept first took shape. By dividing labor into specific, repetitive tasks, these early factories dramatically increased efficiency. This method laid the groundwork for what would later become known as Scientific Management, a systematic approach to optimizing work processes.
As the Industrial Revolution gained momentum, factories became the epicenter of economic activity. They standardized hours and tasks, creating a more regimented work culture. This structure not only boosted productivity but also attracted rural migrants in search of stable employment. As a result, urban populations swelled, leading to profound social changes.
However, the centralized nature of factory work introduced new challenges. Workers faced long hours, often in dangerous and unhealthy conditions. Despite these drawbacks, the factory system fundamentally transformed how goods were produced and how labor was organized.
Key Advancements in Factories
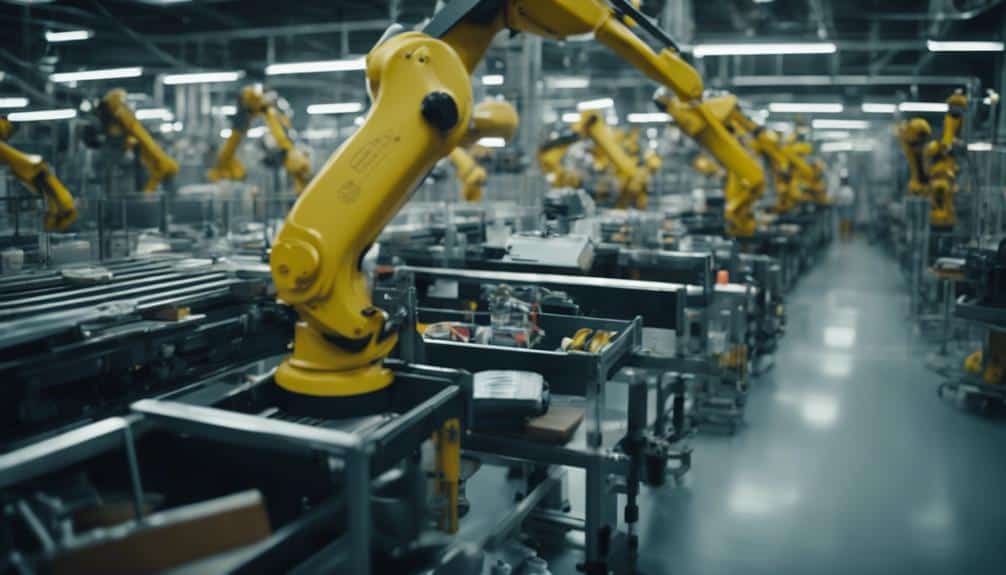
When you consider key advancements in factories, think about how assembly line efficiency redefined production speed and cost.
Scientific management innovations further optimized worker productivity by streamlining tasks.
Additionally, industrial safety measures improved working conditions, setting new standards for employee welfare.
Assembly Line Efficiency
In 1913, Henry Ford's introduction of the assembly line fundamentally transformed factory production by drastically boosting efficiency and slashing production times. The production line allowed workers to perform specialized tasks, which not only improved productivity but also standardized production processes. This meant that vehicles, for example, could be assembled faster and more consistently, leading to mass production of goods.
By focusing on specific, repetitive tasks, workers on the assembly line became highly skilled in their designated roles, enabling factories to produce items at an unprecedented scale. This, in turn, led to lower costs and higher output, making products more affordable for consumers. Additionally, the streamlined production line improved working conditions by reducing the physical strain on workers, who no longer needed to move around the factory floor to complete their tasks.
This innovation marked a significant shift in work culture, emphasizing speed, precision, and division of labor. The assembly line became a model for various industries, illustrating how efficiency could be maximized through methodical organization.
In the broader context of industrial growth, the assembly line was pivotal in shaping modern manufacturing practices, cementing Henry Ford's legacy as a pioneer of industrial efficiency.
Scientific Management Innovations
Frederick Taylor's scientific management transformed factory operations by meticulously analyzing labor processes to maximize efficiency and productivity. When Taylor began his work, factories were grappling with inconsistent output and inefficiencies. By introducing time and motion studies, he identified the most effective ways to perform tasks, which led to standardized procedures across various factory operations.
You might wonder how this impacted the workplace. Factories that adopted Taylor's principles saw a dramatic increase in productivity. Workers were trained to follow specific methods, reducing waste and optimizing their performance. This wasn't just about working harder but working smarter.
Taylor began by breaking down each job into its simplest components, ensuring each task was performed in the best possible way. This systematic approach to work paved the way for modern organizational efficiency. His focus on workplace design, such as arranging tools and materials to minimize unnecessary movement, further streamlined production processes.
Ultimately, Taylor's scientific management set the foundation for contemporary management techniques and work culture principles. His innovations didn't just change how factories operated but also influenced broader industrial practices, ensuring that efficiency and productivity remain central to modern work environments.
Industrial Safety Measures
Factories transformed worker safety by implementing measures like guardrails, emergency stop buttons, and thorough safety training programs. These innovations notably reduced workplace accidents and injuries, creating safer environments for employees. The introduction of safety goggles, helmets, and protective clothing further minimized risks, guaranteeing workers were well-protected against potential hazards.
The Factory Acts of the 19th century played a pivotal role in setting mandatory safety standards. These regulations required factories to adopt specific safety measures to prevent workplace hazards. For example, changes in machinery design, such as the addition of safety guards and automatic shut-off mechanisms, were mandated to enhance worker protection. These advancements not only safeguarded employees but also promoted a culture of safety and responsibility within industrial settings.
Regular safety inspections and maintenance checks became standard practices to identify and rectify potential dangers before they could cause harm. Establishing safety committees within factories ensured ongoing vigilance and continuous improvement in safety protocols. By adhering to these strict measures, factories not only complied with legal requirements but also demonstrated a commitment to their workers' well-being, fostering a more secure and productive work environment.
Labor Division and Efficiency
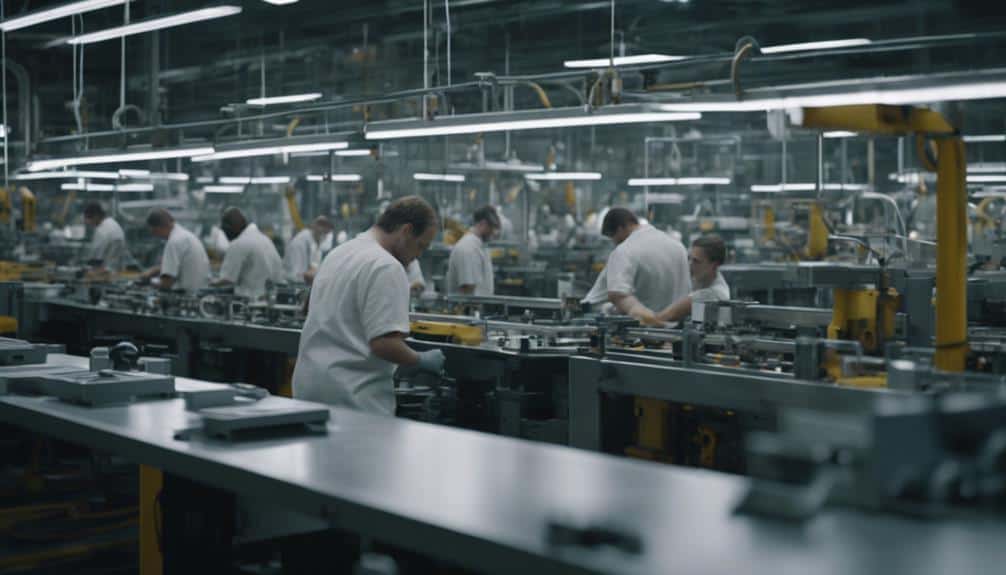
You'll notice that the division of labor in factories dramatically boosted efficiency by assigning specialized roles to workers.
This approach not only increased production rates but also allowed workers to become highly skilled in their specific tasks.
As a result, factories could produce goods faster and at lower costs, fundamentally transforming work culture and economic output.
Task Specialization Benefits
Breaking down complex processes into simpler, specialized tasks in factories has markedly boosted efficiency and productivity. By employing task specialization, workers could focus on specific functions, leading to significant gains in output. When you divide labor, each worker becomes an expert in their assigned task, reducing the time and effort needed to complete it. This structured approach not only enhances individual productivity but also streamlines the entire production process.
The division of labor in factories didn't just improve efficiency; it also paved the way for the mass production of goods. Specialization reduces the need for workers to switch tasks or learn new skills frequently, which minimizes downtime and errors. This systematic organization of work led to lower production costs and higher profitability. As a result, the principles of task specialization and labor division became cornerstones of modern work culture.
The efficiency gains from task specialization in factories revolutionized industrial production processes. You can see how these practices set the stage for contemporary organizational structures, where specialization and division of labor are still critical components. By focusing on specific tasks, workers contribute more effectively to the overall production goals, driving both innovation and economic growth.
Increased Production Rates
The implementation of labor division in factories didn't just enhance individual productivity; it also boosted overall production rates by assigning specific tasks to workers for maximum efficiency. Years ago, when factories started to work on optimizing these processes, they adopted Frederick Taylor's scientific management principles.
Taylor's methods aimed to streamline operations by studying workflows and assigning tasks based on each worker's strengths, thereby minimizing wasted time and effort.
Henry Ford took this a step further with his introduction of the assembly line, which revolutionized manufacturing. By breaking down production into smaller, repetitive tasks, Ford's assembly line drastically increased output while reducing production time significantly.
This method allowed for the mass production of goods at unprecedented speeds, setting a new standard for efficiency.
Moreover, the establishment of specialized departments within factories further improved organizational efficiency. By focusing on specific roles, departments could refine their processes and enhance overall performance.
This specialization not only made factories more productive but also laid the groundwork for modern work culture, emphasizing productivity, efficiency, and task specialization.
Ultimately, these advancements in labor division and efficiency have had a lasting impact, shaping how industries operate and setting the stage for future innovations in productivity.
Impact on Worker Life
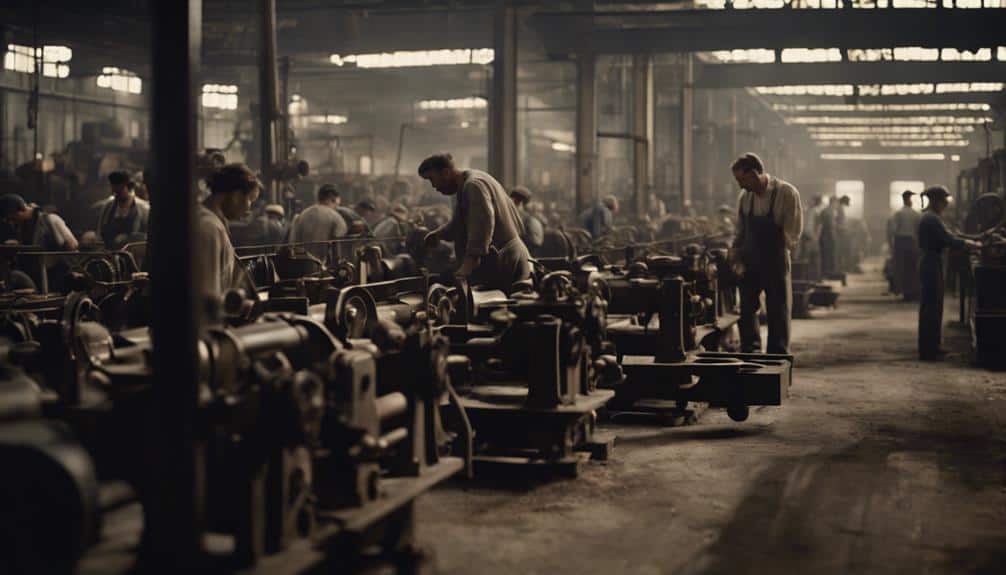
Factories during the Industrial Revolution fundamentally altered workers' lives by imposing grueling hours, hazardous conditions, and rigid hierarchical structures. You'd find yourself working over 12 hours a day, often in environments fraught with danger. The risk of injury or even death was a daily reality. Such conditions weren't just physically taxing; they also disrupted traditional family dynamics.
Men, women, and even children were subjected to harsh labor, leaving little time for family life. Factory work introduced a new level of discipline and surveillance, creating a culture that was both hierarchical and oppressive. You'd be constantly monitored, with strict rules governing your every move. This system reinforced class divisions, as workers were separated from the ownership of production, marking a significant shift towards wage labor.
No longer were you working for yourself or your family; you were part of a broader, more impersonal economic system. The implications of this shift were profound. The factory system didn't just change how people worked; it redefined their entire social structure. By understanding these historical realities, you can better appreciate the complexities and sacrifices that shaped modern work culture.
Evolution of Factory Management
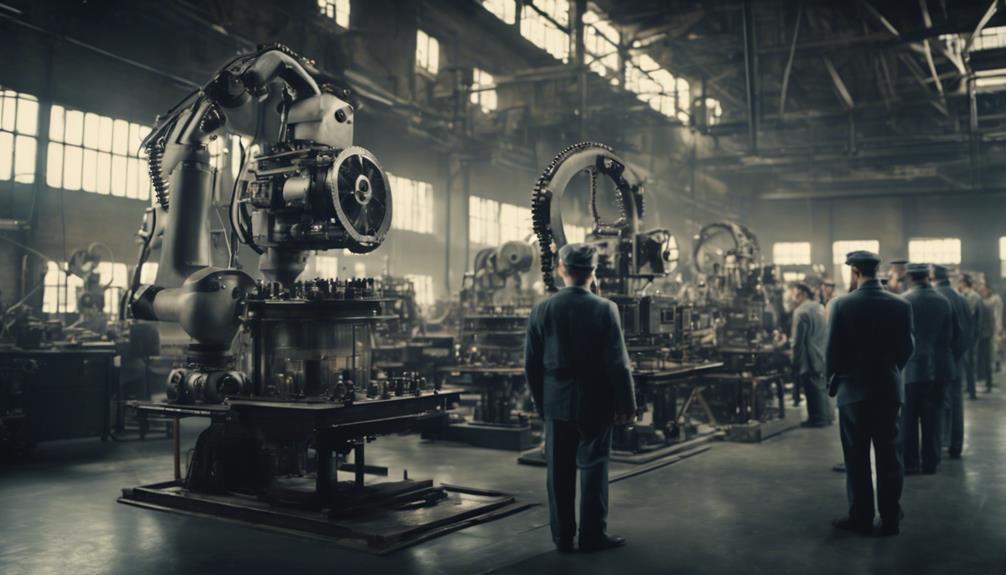
Frequently overlooked yet pivotal, the evolution of factory management during the Industrial Revolution laid the foundation for modern organizational practices by emphasizing efficiency, specialization, and hierarchical structure. In the 18th century, large-scale production and structured work environments emerged, drastically changing how factories operated.
This shift was underscored by Frederick Taylor's Scientific Management principles, which revolutionized factory management. By focusing on efficiency and task specialization, Taylor's methods reduced wasted effort and streamlined processes.
In the early 20th century, Henry Ford's assembly line concept brought further advancements in mass production. By breaking down tasks into simple, repetitive actions, Ford's approach maximized productivity and cemented the importance of specialization within factory management.
Max Weber's Bureaucracy theory also played a vital role, emphasizing clear hierarchies and formalized procedures. These structured environments guaranteed accountability and consistency, principles that are now integral to the modern office.
Technological Innovations
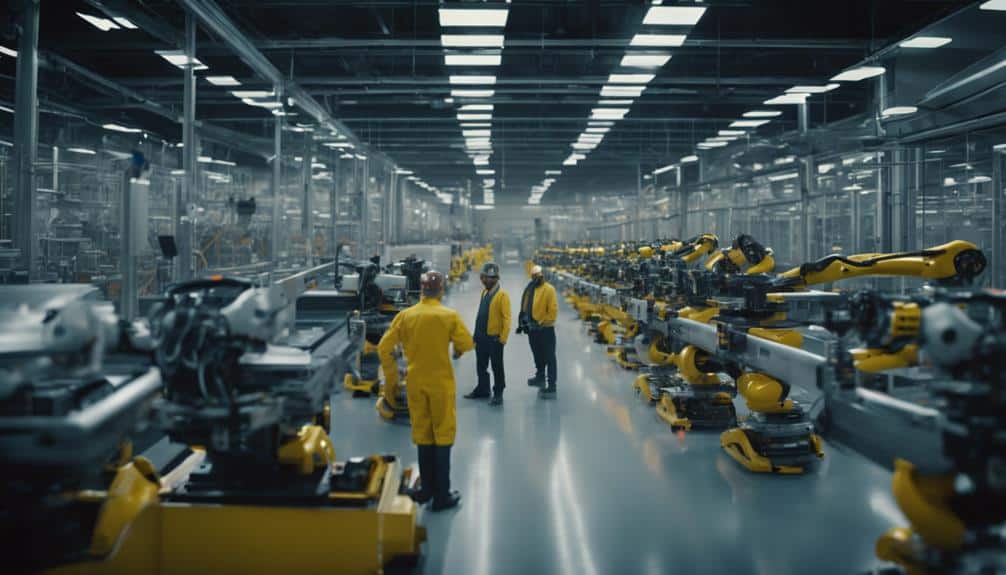
Building on the foundations of organizational practices, technological innovations within factories catalyzed unprecedented leaps in production efficiency and output. The introduction of the steam engine was a game-changer. This powerful machine drastically reduced the reliance on manual labor and natural forces, like water and wind, for driving machinery. Consequently, factories could operate with greater consistency and productivity.
In addition to the steam engine, the implementation of mechanized tools and the assembly line revolutionized production processes. By breaking down complex tasks into simple, repetitive actions, the assembly line enabled workers to produce goods more quickly and uniformly. This shift not only enhanced output but also lowered costs, making products more accessible to the masses.
Moreover, factories became innovation hubs, continually integrating new machinery and techniques to streamline operations. As technology advanced, the nature of work within factories evolved. For instance, the rise of automation and digital controls has enabled some aspects of production to be managed remotely. This flexibility has redefined traditional work practices, illustrating that technological advancements in factories have far-reaching implications beyond their walls.
Ultimately, these innovations laid the groundwork for the mass production of goods, shaping the modern industrial landscape and work culture.
Factories and Urbanization
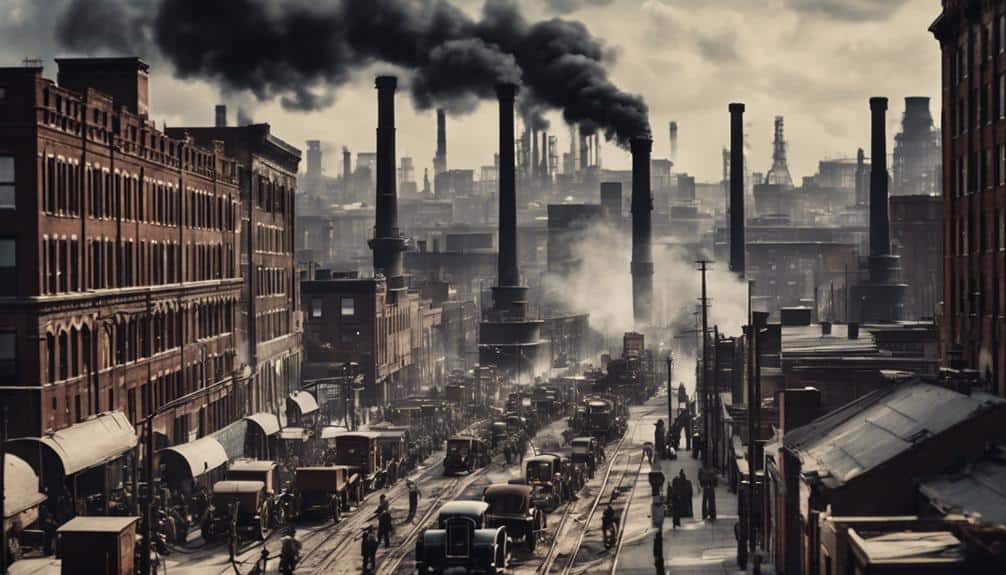
The migration of workers from rural areas to burgeoning urban centers defined the urbanization wave and underscored the transformative impact of factories on modern work culture. As people moved in search of factory jobs, urban landscapes evolved dramatically. Cities expanded with industrial areas, giving rise to the mass production of goods and pushing the boundaries of efficiency and output.
You're probably aware that this shift wasn't just about geography—it reshaped economies and societal structures. Factories became hubs of economic activity, drawing more workers and creating a self-sustaining cycle of growth and urbanization. This concentration of labor and industry in cities didn't just change where people lived, but also how they worked and interacted.
Urbanization brought about more than just economic benefits; it also fostered the development of modern organizational structures. The factory environment necessitated hierarchy, time management, and specialized roles, which collectively contributed to the foundation of contemporary work culture.
In short, factory jobs were a catalyst for urbanization, leading to the rapid growth of cities and the transformation of societal norms. This migration marked the beginning of a new era, where industrialization and urban living became the norm.
Global Spread of Factories
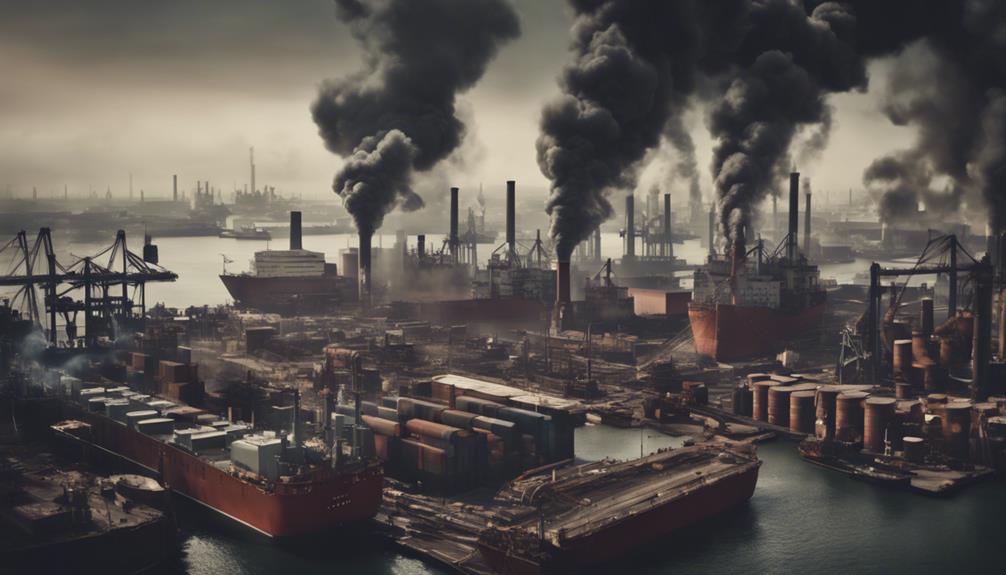
As factories proliferated globally during the Industrial Revolution, they fundamentally reshaped labor practices and catalyzed a shift from agrarian to industrial economies. This global spread of factories introduced mass production and assembly lines, enabling workers to collaborate more efficiently.
You saw entire communities transform as people moved from rural areas to urban centers, drawn by the promise of consistent work and wages.
Factory work required a labor force that could handle the demands of standardized work hours and repetitive tasks. This new dynamic led to the creation of a more organized and disciplined workforce, essential for maintaining productivity on the factory floor.
By working together, employees could achieve greater output than ever before, marking a significant departure from the individualized labor of agrarian societies.
However, this shift wasn't without its challenges. The concentration of workers in factories also led to overcrowded living conditions and sparked labor movements as workers fought for better wages, hours, and working conditions. These movements were pivotal in shaping the foundation of modern industrial societies.
The global spread of factories not only revolutionized production but also laid the groundwork for the labor rights we recognize today.
Modern Factory Practices
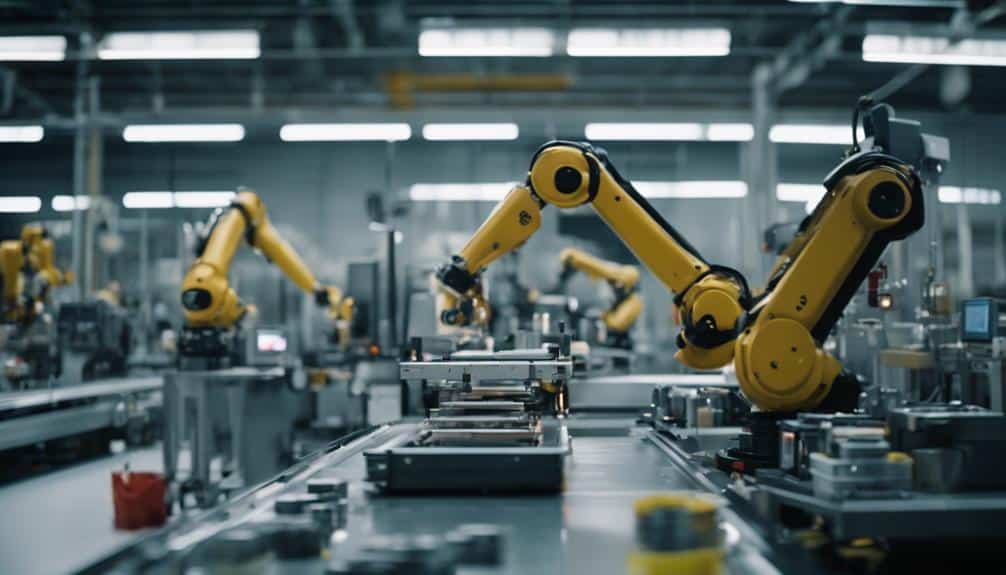
Amid the evolving landscape of industrialization, modern factory practices emerged, revolutionizing work culture through the implementation of assembly lines, specialized tasks, and efficient production methods. With the advent of these innovations, factories began to maximize productivity by adopting time management systems, strict schedules, and standardized processes. This shift transformed traditional artisanal methods into highly organized and mechanized operations.
The introduction of machinery and automation played a pivotal role in this transformation. By dividing labor into specialized tasks, factories could streamline operations and notably increase output. This efficiency came at a cost, however, as factory workers often faced long hours, poor working conditions, and limited rights during the early phases of industrialization.
Despite these challenges, modern factory practices laid the groundwork for contemporary organizational structures, hierarchies, and management strategies. The focus on efficiency and productivity reshaped the concept of work and began fostering company loyalty among employees. Workers became integral parts of the production process, contributing to a more cohesive and efficient workplace.