From revolutionizing infrastructure and transportation to driving wartime industrial output, steel's journey from the Bessemer process to the formation of U.S. Steel has been transformative.
Discover how this mighty material, despite facing global competition and environmental challenges, remains a cornerstone of modern industry.
Historical Roots of Iron and Steel
The iron and steel industry in America traces its origins back to 1647 when ironmaking began in Saugus, Massachusetts. This early effort laid the foundation for what would become a pivotal sector in American industry.
As you explore the historical roots, you'll find that the 19th century was a transformative period. The discovery of vast iron ore deposits in the northern Great Lakes region greatly boosted iron production, setting the stage for subsequent advancements.
The introduction of the Bessemer process in 1855, although revolutionary, was only one piece of the puzzle. Andrew Carnegie, a titan in the industry, made strategic investments in steelworks, including the Edgar Thomson Works in Braddock, Pennsylvania. His efforts were instrumental in scaling up steel production, making steel a dominant material in construction and manufacturing.
Further consolidation came with the formation of the U.S. Steel Corporation in 1901, spearheaded by J. P. Morgan. This move centralized control and optimized efficiencies across the industry.
Understanding these historical elements provides you with a thorough view of how iron and steel evolved from modest beginnings to industrial giants, shaping America's economic landscape.
The Bessemer Process Revolution
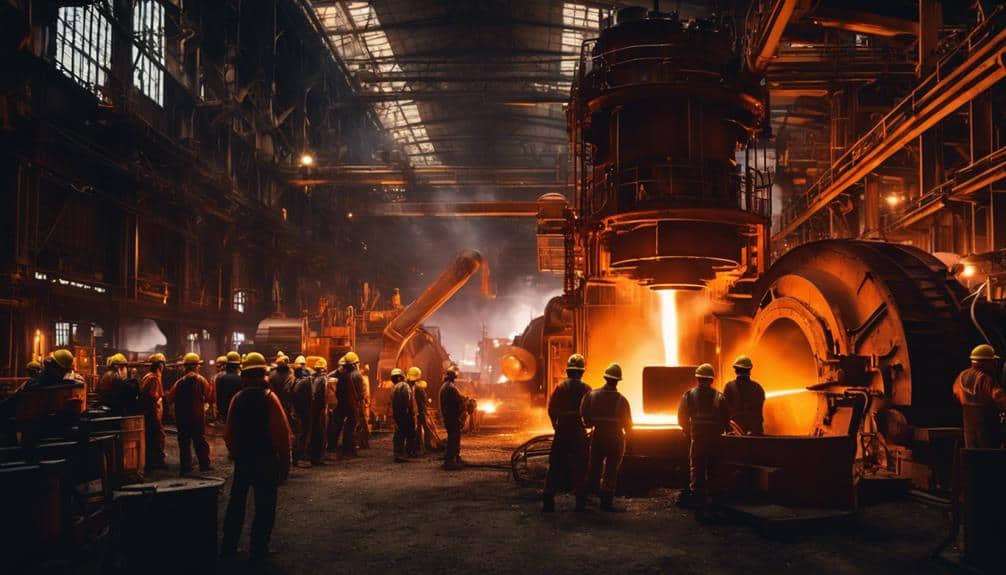
You'll find that the Bessemer process, introduced in 1855, fundamentally transformed steel production. By blowing air through molten iron to eliminate impurities, it increased production efficiency and reduced costs dramatically.
This technological breakthrough enabled high-volume steel production, fueling industrial growth and positioning the United States as a global steel leader.
Efficiency and Cost Reduction
By adopting the Bessemer process, you can immensely cut steel production costs while boosting efficiency by eliminating impurities from molten iron. This method revolutionized steel production, streamlining the process to produce high-quality steel rapidly and economically. The Bessemer process, which involves blowing air through molten iron, removes impurities like carbon, silicon, and manganese, transforming it into superior steel.
In 1873, the Bethlehem Iron Company incorporated this groundbreaking technology, marking a pivotal moment in the industrial revolution. By leveraging the Bessemer process, they optimized efficiency and achieved a substantial cost reduction. This was a game-changer for steel production, as it enabled mass production on an unprecedented scale. The data speaks volumes: production times were slashed from days to mere hours, and costs plummeted, making steel more accessible and affordable.
The Bessemer process's impact on the industrial revolution can't be overstated. It catalyzed advancements in various sectors, including construction, transportation, and infrastructure. By greatly reducing production costs and enhancing efficiency, the Bessemer process paved the way for the modern steel industry.
Your understanding of this revolutionary method will underscore how critical it was in shaping industrial capabilities and economic landscapes.
High-Volume Steel Production
In adopting the Bessemer process, you revolutionize high-volume steel production by reducing time and costs, thereby transforming industrial capabilities.
Developed by Henry Bessemer in 1855, this method involves blowing air through molten iron to oxidize and remove impurities, converting it into steel.
By streamlining steel production, you achieve a significant reduction in both cost and time, which directly influences the steel industry's expansion.
The efficiency of the Bessemer process enables mass production of steel, essential for various sectors like railroads and construction.
Prior to this, producing steel was labor-intensive and expensive, limiting its application.
With the introduction of the Bessemer process, you can produce steel on a scale previously unimaginable, driving industrial growth and innovation.
Data shows that the Bessemer process slashed production times from days to mere hours, and costs plummeted by up to 80%.
This efficiency not only made steel more accessible but also catalyzed rapid development across industries.
The steel industry, bolstered by this method, experienced unprecedented growth, becoming a cornerstone of the Industrial Revolution.
Technological Breakthrough Impact
Revolutionizing the steel industry, the Bessemer Process drastically reduced production costs and time, enabling unprecedented industrial growth. By blowing air through molten iron, this technological breakthrough removed impurities efficiently, transforming raw iron into high-quality steel swiftly. Prior to this, steel production was prohibitively expensive and labor-intensive, stifling industrial development. The Bessemer Process, introduced in 1855, changed that narrative, facilitating mass production and making steel a cost-effective material for a multitude of applications.
The impact of the Bessemer Process on industrial development is profound and multifaceted:
- Efficiency: Reduced the time to produce steel from days to mere hours.
- Cost-Effective: Lowered the cost of steel production, making it accessible for widespread use.
- Mass Production: Enabled the large-scale manufacture of steel, fueling growth in industries like construction and transportation.
- Quality Improvement: Produced consistently high-quality steel, essential for demanding applications.
- Industrial Expansion: Catalyzed the growth of industries by providing a reliable and affordable steel supply.
For those seeking to understand the evolution of modern industry, recognizing the Bessemer Process's role in advancing steel production is essential. This process marked a pivotal shift, laying the groundwork for the industrial era's explosive growth and technological advancements.
Andrew Carnegie's Impact
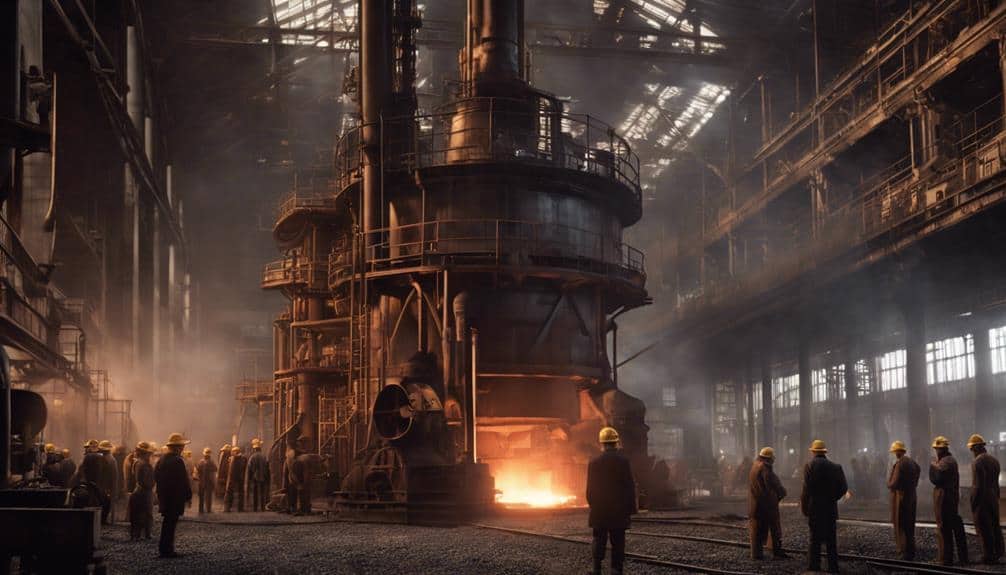
You'll see Carnegie's impact clearly when examining his vertical integration strategy, which optimized every stage of steel production, from raw materials to distribution.
His flagship plant, Edgar Thomson Steel Works, epitomized technological innovation and operational efficiency, setting new industry standards.
Carnegie's legacy in steel production is underscored by his empire's eventual consolidation into U.S. Steel Corporation.
Vertical Integration Strategy
Leveraging a vertical integration strategy, Andrew Carnegie controlled every aspect of the steel production process, from mining iron ore to manufacturing and transportation, guaranteeing unparalleled efficiency and cost savings. By owning the entire supply chain, Carnegie achieved a level of industry dominance that was unparalleled. His approach allowed him to streamline operations and reduce reliance on external suppliers, translating directly into lower production costs and improved product quality.
Carnegie's vertical integration encompassed several critical components:
- Ore Mines: Securing raw materials at the source eliminated middlemen and price fluctuations.
- Steel Mills: Owning state-of-the-art mills ensured peak production capacity and technological advancements.
- Transportation Networks: Controlling railroads and shipping lines minimized logistics costs and delays.
- Distribution Channels: Direct sales to consumers and industries enhanced market reach and customer satisfaction.
- Labor Management: Implementing efficient HR practices reduced labor disputes and increased productivity.
Technological Innovations Legacy
Building on his mastery of vertical integration, Andrew Carnegie's technological innovations, such as the adoption of the Bessemer process, fundamentally transformed the efficiency and scale of steel production. By implementing the Bessemer process at facilities like the Edgar Thomson Works in Pennsylvania, Carnegie achieved unprecedented production speeds and cost reductions. This innovation allowed for the mass production of steel, dramatically lowering per-unit costs and making steel more accessible for infrastructure development.
Carnegie's foresight didn't stop there. He continuously invested in cutting-edge technologies and processes, ensuring his steel manufacturing operations remained at the industry's forefront. His focus on technological advancements not only enhanced output but also improved product quality, setting new standards within the steel industry. The impact of these innovations extended far beyond his mills, contributing to the construction of iconic structures that defined an era of rapid industrial growth.
Through these strategic moves, Carnegie's legacy in the steel industry remains indelible. His emphasis on technological innovation has shaped modern steel manufacturing, making it more efficient and scalable. Today, his contributions continue to influence infrastructure development, underscoring the lasting impact of his pioneering efforts in steel production.
Rise of U.S. Steel Corporation
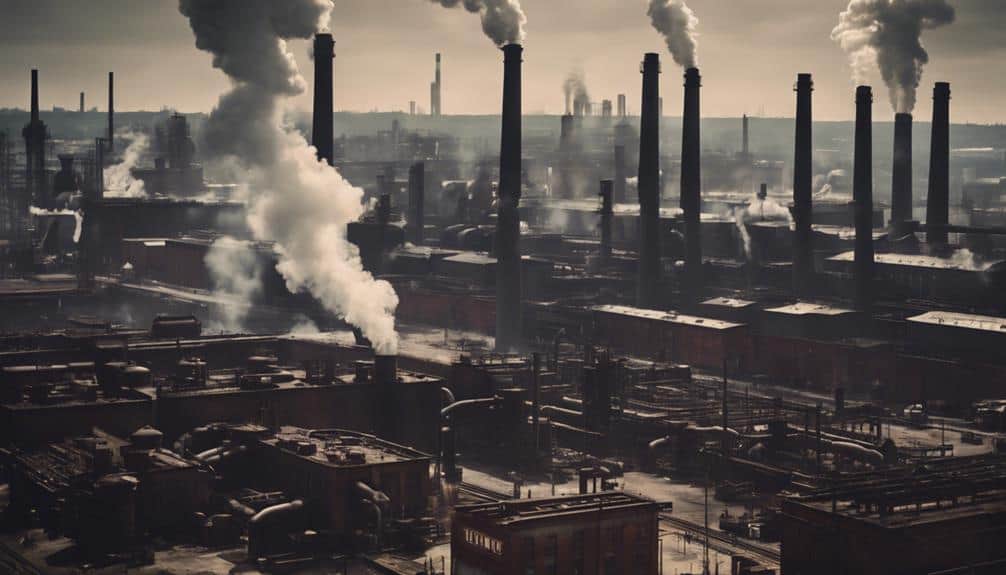
In 1901, the formation of U.S. Steel Corporation through a merger of leading steel companies marked the creation of the world's first billion-dollar enterprise, fundamentally reshaping the industrial landscape. As the largest steel company globally, United States Steel Corporation consolidated major players like Carnegie Steel under the leadership of Charles Schwab. This merger enabled unprecedented control over raw materials, production, and distribution.
Key elements of U.S. Steel's dominance included:
- Integration of blast furnace technology: Advanced smelting processes increased efficiency and output.
- Economies of scale: Large-scale operations reduced costs and improved competitiveness.
- Vertical integration: Control over the entire supply chain from raw materials to finished products.
- Research and development: Continuous innovation to improve steel quality and production methods.
- Market influence: Significant leverage over steel prices and industry standards.
U.S. Steel's formation was a cornerstone in transforming steel producers into industrial giants. By the 1970s, the company had reached peak output, reflecting its status as the bedrock of American industry. However, challenges emerged, leading to its removal from the Dow Jones Industrial Average in 1991. Today, U.S. Steel faces a bidding war among rivals like Cleveland-Cliffs, Esmark, and ArcelorMittal, underscoring its pivotal yet uncertain role in the industry.
Global Steel Production Advances
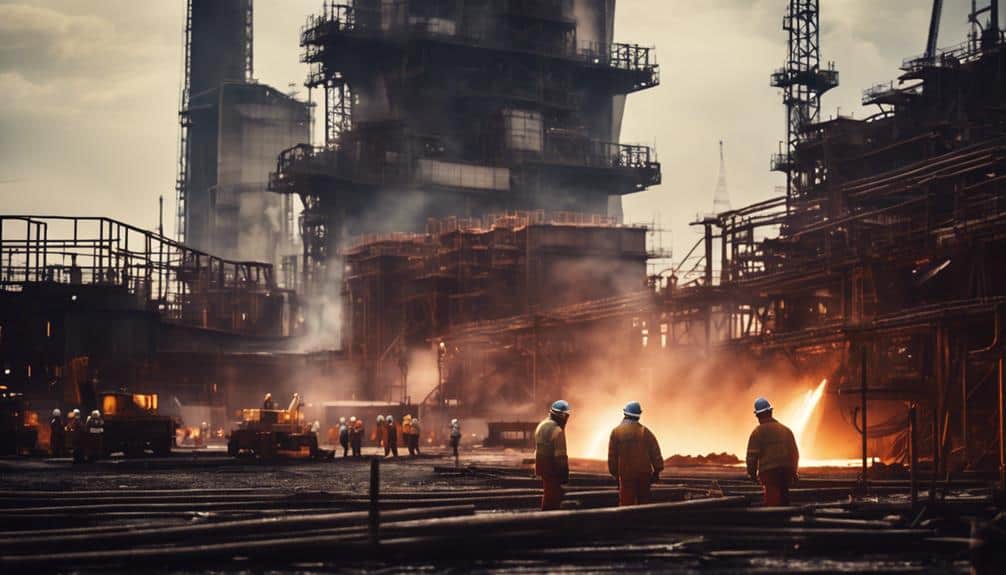
Technological advancements like electric arc furnaces and basic oxygen furnaces have transformed global steel production, with China leading the charge by producing over half of the world's steel output. These innovations have streamlined the steelmaking process, enhancing energy efficiency and reducing production costs.
As a result, countries like India, Japan, and South Korea have also seen steady growth in their steel production, contributing significantly to the global output.
The global steel industry is increasingly focused on sustainable practices. Companies are adopting energy-efficient technologies and implementing robust recycling initiatives to minimize their environmental impact. For instance, electric arc furnaces utilize scrap steel, reducing the need for raw materials and lowering emissions.
This shift towards sustainability is driven by the demand in sectors such as construction, automotive, and infrastructure, which require high-quality, eco-friendly steel products.
As the construction sector continues to expand, the need for durable and sustainable steel products grows. Innovations in steel production ensure that the industry can meet this demand while adhering to stringent environmental standards.
The global output of steel isn't just about quantity but also about producing steel in a way that supports long-term ecological balance.
Steel in the World Wars
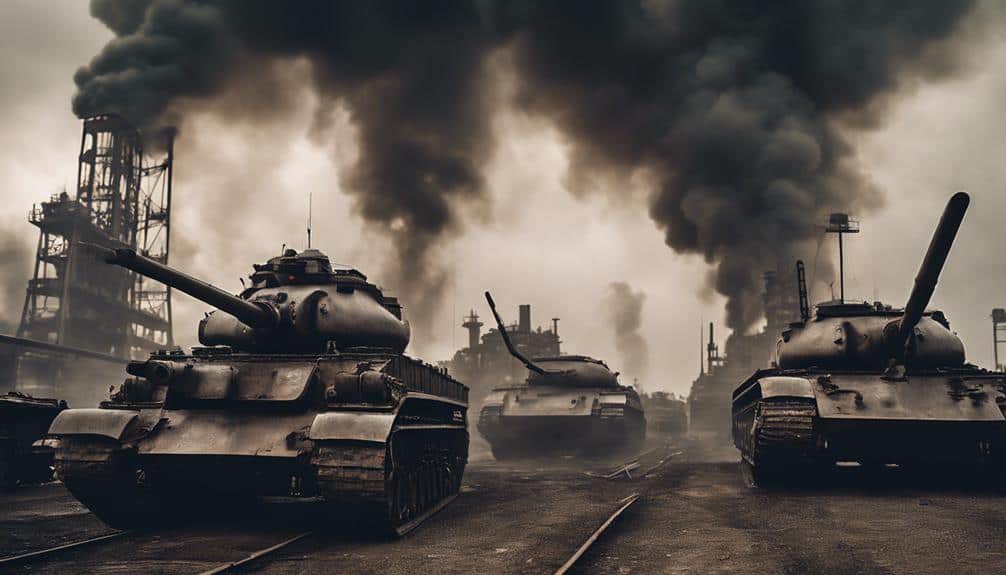
Steel played a central role in both World War I and World War II, greatly influencing the outcomes through its application in munitions, ships, and military infrastructure. During these conflicts, Bethlehem Steel emerged as a cornerstone of the war effort. In World War I, the company ramped up the production of iron and steel products, becoming a major supplier of munitions.
By World War II, Bethlehem Steel had received over $1.3 billion in orders for ammunition and war materials, solidifying its international steel dominance. Bethlehem Steel's contributions to the war effort included:
- Doubling its workforce to meet the massive demand for steel products.
- Becoming the world's largest supplier of ships, essential for naval supremacy.
- Supplying steel for military infrastructure and iconic structures like the University of Pittsburgh's Cathedral of Learning.
- Collaborating with the United Steelworkers to guarantee efficient production.
- Producing steel rails essential for transporting troops and materials.
The company's efforts weren't isolated; they were part of a broader industrial mobilization that saw the transformation of steel manufacturing capabilities across the globe. The production of steel during these wars didn't just fuel battles; it laid the groundwork for the modern industrial world.
Post-War Industry Shifts
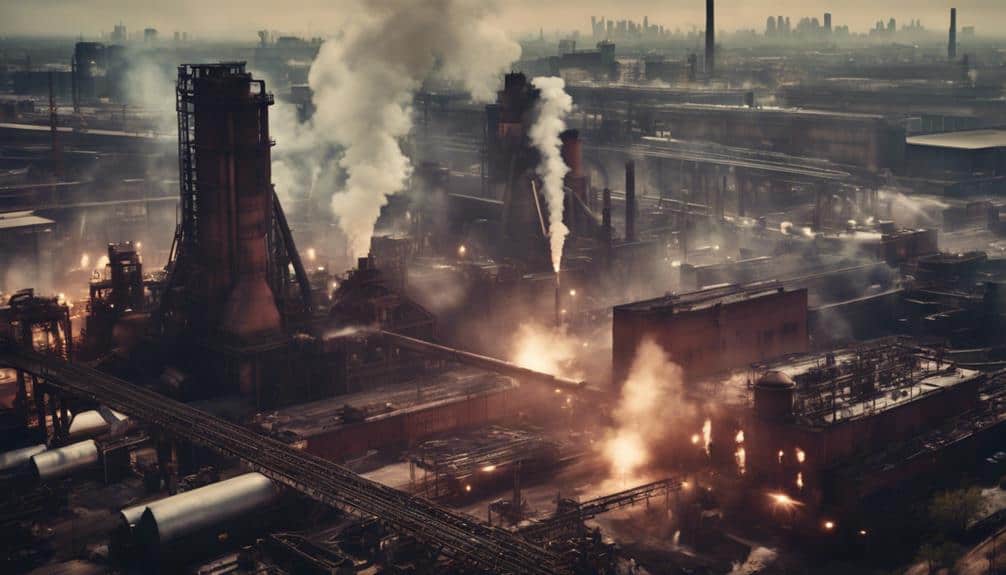
Following the wartime boom, steelmakers like US Steel faced increasing competition from Japan and Germany, who'd embraced more efficient steelmaking technologies, fundamentally changing the industry's dynamics. In the post-war period, these foreign rivals utilized innovations like the Basic Oxygen Furnace (BOF), which notably reduced production costs and enhanced output efficiency. Meanwhile, US Steel struggled to modernize, leading to a decrease in market share.
Concurrently, the emergence of mini-mills in the United States marked a pivotal industry transformation. These nonunion competitors utilized electric arc furnaces (EAFs) to melt scrap steel, providing a more adaptable and cost-efficient production approach compared to traditional integrated mills. Nucor, a pioneer in mini-mill technology, exemplified this shift. By the 1980s, Nucor had exceeded US Steel in both production and market value, highlighting the significant changes within the steel industry.
This evolution not only impacted US Steel's dominance but also indicated a broader economic shift. The adoption of EAFs by mini-mills eroded the market position of traditional steelmakers, reshaping the competitive landscape. The post-war era therefore marked a crucial moment in the ongoing evolution of the steel industry.
Modern Steel Challenges
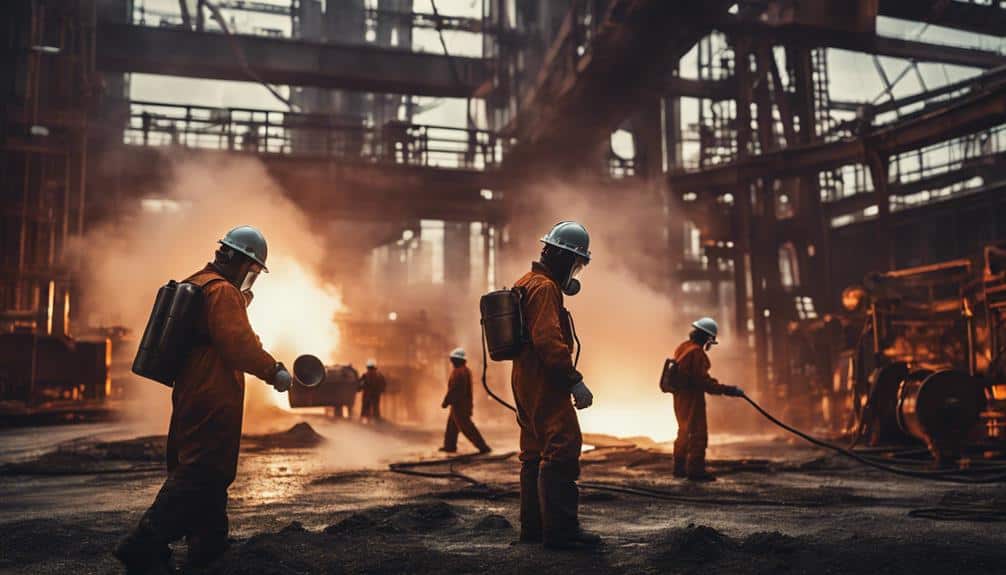
Traversing the modern steel landscape, manufacturers face heightened competition from global markets, pressing environmental regulations, and the need to adapt to innovative technologies like electric arc furnaces. The influx of steel from foreign markets such as China and Japan intensifies price pressures and demands improved production efficiency. You must maneuver these complexities while adhering to stringent environmental concerns, particularly around carbon emissions and waste disposal.
Technological advancements like electric arc furnaces challenge traditional blast furnace operations, necessitating significant capital investment and technical expertise. Labor issues, including union demands and workforce restructuring, further complicate the industry's dynamics. Global economic shifts and fluctuating trade policies add layers of unpredictability, impacting both competitiveness and sustainability.
Consider the following factors that steel manufacturers must address:
- Foreign markets: Competing with lower-cost imports from steel giants like China and Japan.
- Environmental concerns: Meeting carbon emission targets and managing waste effectively.
- Technological advancements: Adapting to electric arc furnaces and other modern methods.
- Labor issues: Balancing union negotiations and adjusting to workforce changes.
- Global economic shifts: Navigating volatile trade policies and economic climates.
You need to stay agile and innovative to thrive in this ever-evolving industry landscape.