Discover how trailblazing inventions like the flying shuttle, spinning jenny, and power loom ignited the textile boom, transforming weaving and spinning efficiency.
Uncover the revolutionary impact of these advancements on global trade and economic growth.
Early Industry Developments
The early developments of the textile industry were catalyzed by the East India Company's production of cotton goods in South Asia for the burgeoning UK market. This demand spurred innovations that would transform textile manufacturing.
Mechanized production took center stage with inventions like the spinning jenny, which notably increased yarn production by allowing multiple spindles to be operated by a single worker. This was followed by the water frame, a pivotal invention that harnessed water power to drive spinning machinery, greatly enhancing efficiency.
You can't overlook the critical role of the spinning mule, which combined features of the spinning jenny and the water frame. This hybrid machine produced finer and stronger yarn, essential for high-quality textiles. The rapid growth in cotton production, driven by these technological advancements, positioned Lancashire as a key industry hub, benefiting from its humid climate and established wool industry.
The 1700 and 1721 Calico Acts, which banned the import and sale of finished cotton goods, inadvertently fostered the growth of a domestic mechanized cotton industry. This legislative push, combined with groundbreaking inventions, laid the groundwork for a revolution in textile manufacturing, setting the stage for the Industrial Revolution.
The Flying Shuttle
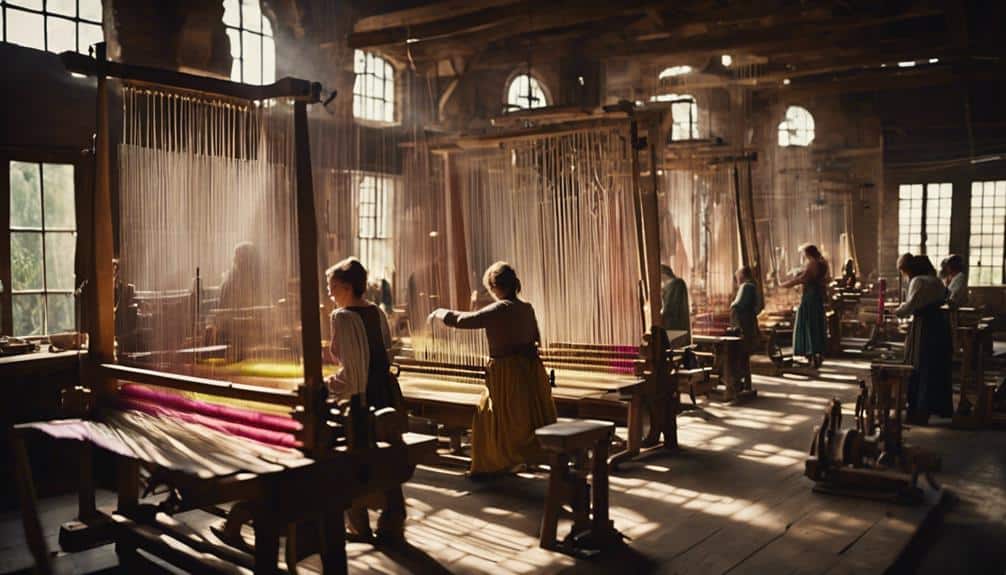
John Kay's 1733 invention of the flying shuttle marked a pivotal moment in textile history, dramatically enhancing weaving efficiency and productivity. This ingenious device allowed a single weaver to operate a loom and produce wider fabrics, a feat previously requiring two people. By mechanizing the process of passing the shuttle through the loom's threads, Kay's innovation eliminated the need for manual shuttle-passing, enabling faster and more consistent weaving.
The impact of the flying shuttle can't be overstated. It revolutionized the textile industry by:
- Increasing productivity and efficiency, enabling weavers to produce more fabric in less time.
- Reducing labor costs, as fewer workers were needed to achieve the same or greater output.
- Paving the way for further mechanization during the Industrial Revolution.
With the flying shuttle, the textile industry witnessed a significant leap in productivity. Weavers could now produce wider fabrics more quickly, meeting the growing demand for textiles. This not only boosted the industry's output but also laid the groundwork for subsequent innovations that further propelled the Industrial Revolution.
The flying shuttle represents a cornerstone in the journey towards modern textile manufacturing, illustrating how a single invention can transform an entire industry.
Spinning Jenny and Water Frame
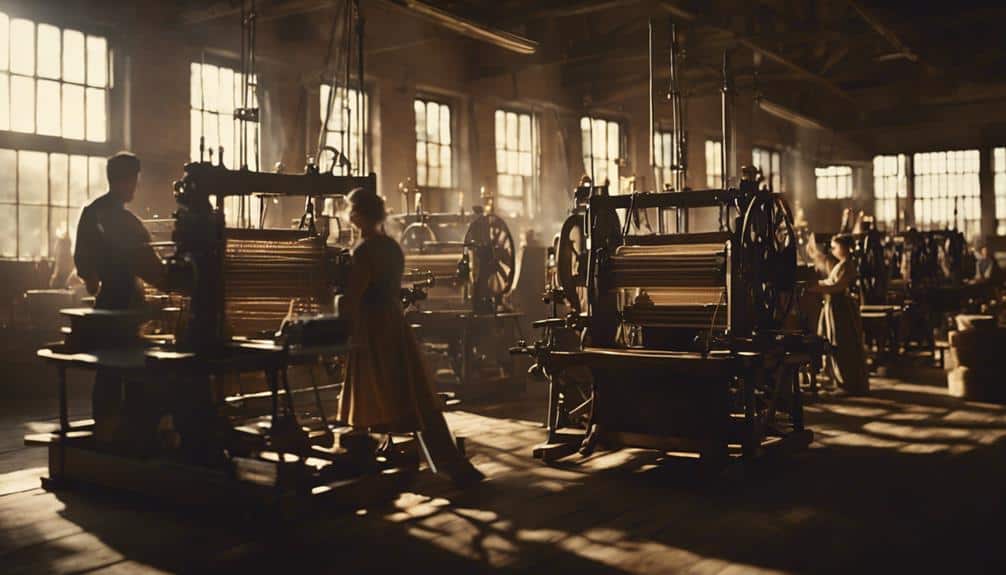
Building on the momentum generated by the flying shuttle, the Spinning Jenny and Water Frame further revolutionized textile production by vastly increasing the efficiency and scale of yarn spinning. James Hargreaves' Spinning Jenny, invented in 1764, allowed a single operator to spin multiple threads simultaneously, greatly boosting productivity. This innovation reduced labor by enabling one person to manage several spindles at once, making yarn production faster and more cost-effective.
This innovation reduced labor by enabling one person to manage several spindles at once, making yarn production faster and more cost-effective.
Meanwhile, Richard Arkwright's Water Frame, developed in 1769, took mechanization to another level. By using water power, Arkwright's invention mechanized yarn spinning, producing stronger, high-quality yarn suitable for warp threads. The Water Frame significantly lowered production costs and enhanced the overall efficiency of the textile industry. Factories equipped with Water Frames utilized horse and water power, marking a critical shift towards industrialization.
Both the Spinning Jenny and Water Frame were pivotal in transforming the textile industry. They led to increased output and reduced costs, laying the groundwork for modern textile manufacturing.
Together, these innovations exemplified the powerful impact of mechanization on yarn spinning, setting the stage for further advancements in textile production.
The Spinning Mule
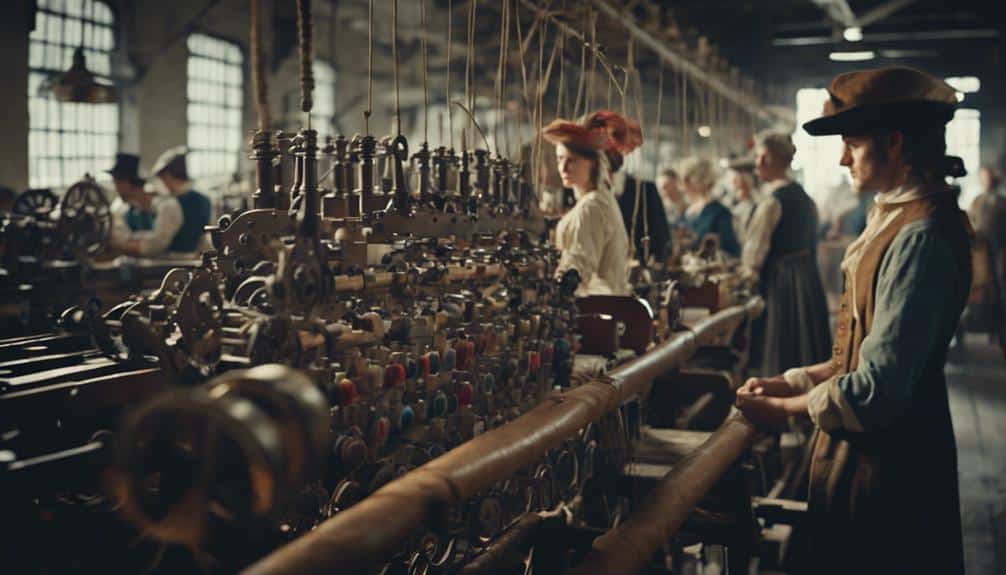
Samuel Crompton's Spinning Mule, introduced in 1779, masterfully merged the functionalities of the Spinning Jenny and Water Frame, forging a new era in textile manufacturing by enabling the production of finer and stronger threads at an unprecedented efficiency and cost-effectiveness. By blending these spinning technologies, Crompton's innovation revolutionized thread production, particularly for calico cloth. The Spinning Mule allowed for the creation of warp threads that were both durable and delicate, greatly improving the quality and versatility of textile products.
The Spinning Mule became a cornerstone in the textile manufacturing process during the Industrial Revolution. Its ability to produce superior threads at lower costs transformed the industry, making high-quality fabrics more accessible and driving economic growth. Samuel Crompton's invention didn't just enhance productivity; it also set a new standard for thread quality, making it an indispensable tool for manufacturers.
Consider the profound impact of the Spinning Mule:
- Economic Empowerment: Lower production costs increased profitability for manufacturers and affordability for consumers.
- Quality Revolution: Finer, stronger threads elevated the standard of textile products.
- Industrial Momentum: Accelerated advancements in textile manufacturing during the Industrial Revolution.
These factors underscore why the Spinning Mule was a pivotal advancement in the history of textile manufacturing.
Power Loom Advancements
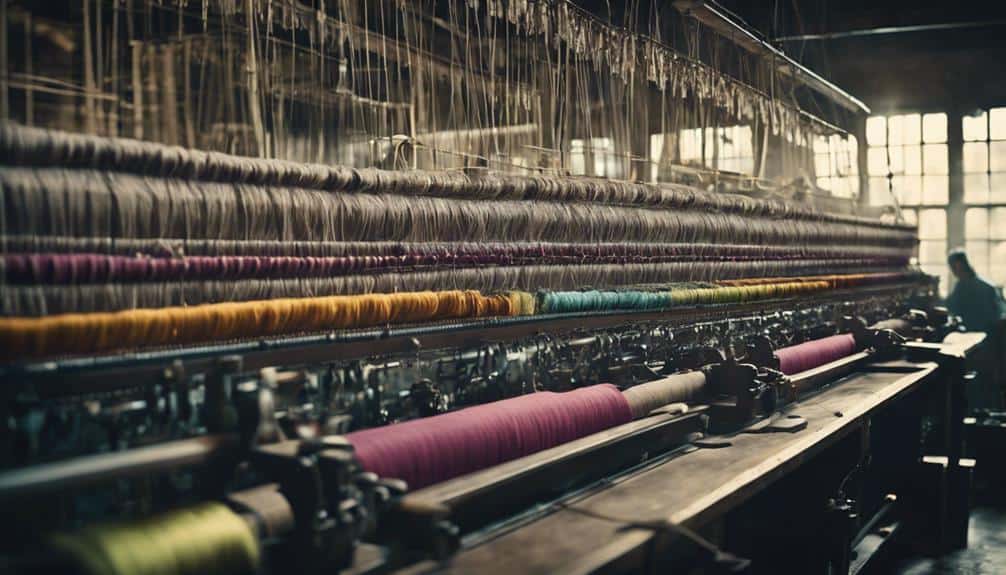
You'll find that the journey of power loom advancements begins with Edmund Cartwright's invention in 1785, which initially faced numerous challenges.
Samuel Horrocks' improvements in 1813 addressed many of these issues, leading to greater efficiency.
Cartwright's Loom Challenges
Edmund Cartwright's early power loom, despite its innovative approach, encountered notable technical challenges, particularly with thread breakage, which highlighted the complexities of mechanizing textile production. The vertical power loom, while groundbreaking, struggled with maintaining thread integrity, leading to frequent stoppages and inefficiencies. This issue underscored the intricate balance required in textile manufacturing between mechanical components and delicate threads.
You can imagine the frustration:
- Frequent thread breaks: Disrupting production flow and increasing downtime.
- Technical limitations: Early designs couldn't handle the delicate nature of the threads.
- Economic pressures: Loom failures translated into financial losses for manufacturers.
Samuel Horrocks made strides in power loom design by patenting a more reliable version in 1813, partially addressing Cartwright's challenges. Yet, it was Richard Roberts who truly revolutionized the field in 1822. His enhancements to the power loom design notably increased efficiency and reliability. Roberts' partnership with Roberts Hill & Co. facilitated the mass production of these improved looms, fundamentally transforming textile manufacturing.
Cartwright's initial struggles laid the groundwork for these critical advancements. By understanding the technical hurdles he faced, you gain a deeper appreciation for the subsequent innovations that wove the fabric of modern textile production.
Horrocks' Successful Improvements
Building on Cartwright's initial innovations, the significant advancements made by Samuel Horrocks in 1813 addressed the persistent issue of thread breakage, setting the stage for a major leap in power loom technology. Horrocks' improvements were pivotal in overcoming a critical flaw that plagued earlier loom designs, directly impacting the textile industry's efficiency.
By tackling the thread breakage problem, Horrocks' power loom enhancements ensured smoother operation and reduced downtime, which had been a significant bottleneck. This breakthrough meant that textile manufacturers could produce more fabric with less interruption, substantially increasing productivity.
You can appreciate how this innovation complemented the earlier development of the spinning jenny, which had already revolutionized yarn production. Horrocks' work seamlessly integrated with these advancements, creating a more cohesive and efficient textile manufacturing process.
While Richard Roberts would later refine these designs in 1822, Horrocks' contributions laid the essential groundwork. His focus on efficiency not only improved the power loom's functionality but also set new standards for the industry. These advancements were instrumental in driving the textile boom, making it possible to meet the growing demand for fabrics and fostering further innovations in the field.
Roberts' Mass Production
Following Horrocks' groundwork, Richard Roberts' 1822 enhancements to the power loom greatly advanced textile manufacturing by enabling mass production and dramatically increasing weaving efficiency. Roberts' ingenious improvements transformed the landscape of the textile industry, making it possible to produce fabric at unprecedented scales. His work didn't just tweak existing designs; it created a leap in technological capability that propelled the industry into a new era.
Roberts, Hill & Co. took these advancements to the next level by successfully mass-producing the enhanced power looms. This move was pivotal as it made the technology widely accessible, spurring a wave of industrialization across textile centers. The innovations made by Roberts played a crucial role in the industrial revolution, marking a significant shift from manual labor to mechanized processes.
Consider the impact of these innovations:
- Increased productivity: The power loom could weave fabric much faster than traditional methods, boosting overall output.
- Reduced labor costs: With machines doing the work, the need for manual labor decreased, lowering production costs.
- Economic growth: The efficiency and scale of production contributed to the economic expansion of textile hubs.
Understanding Roberts' contributions offers a window into the transformative power of industrial advancements, underscoring how innovation drives progress.
Steam Engines in Mills
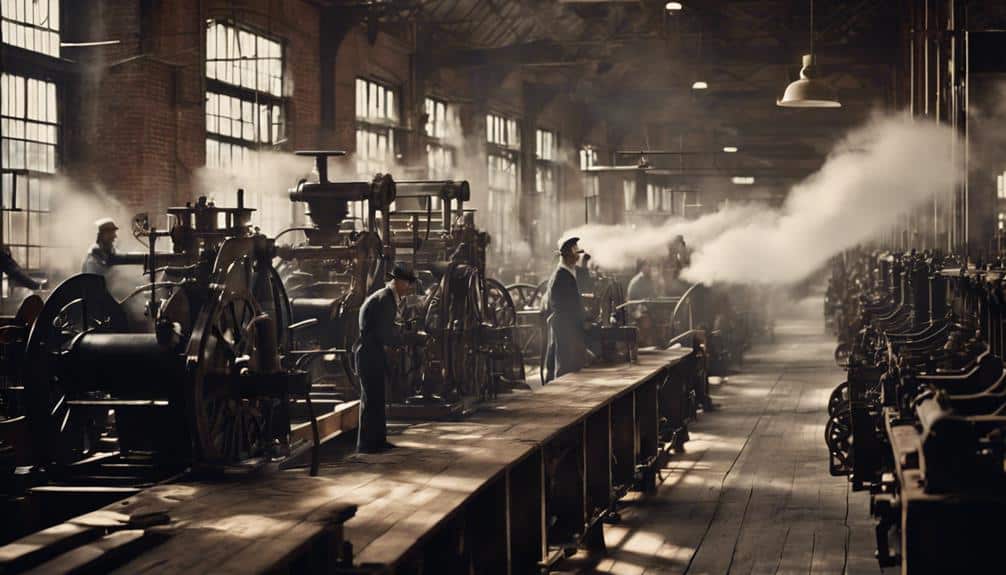
You'll find that the introduction of steam engines in mills marked a significant change in textile production.
By shifting to steam power, mills achieved unprecedented efficiency, no longer tethered to water sources.
This advancement not only boosted production rates but also transformed the industry's economic landscape, particularly in regions like Lancashire.
Steam Engine Efficiency
Steam engines, with their unparalleled efficiency, revolutionized textile mills by drastically increasing production speed and output. By providing a reliable power source, steam engines enabled mills to operate continuously and on a larger scale, driving remarkable productivity gains.
The efficiency of steam engines meant that textile mills could churn out more fabric in less time, significantly boosting the industry's output. This leap in productivity was a cornerstone of the Industrial Revolution, transforming mills into powerhouses of production.
Consider the impact of steam engine efficiency on the textile industry:
- Unmatched Production Speed: Mills could now produce textiles at a pace never seen before, meeting growing market demands.
- Continuous Operation: The ability to run mills around the clock meant a dramatic increase in overall output.
- Economic Growth: More efficient mills contributed to rapid industrial expansion and job creation.
Steam engines didn't just power machinery; they powered progress. They allowed textile mills to break free from the limitations of previous power sources, fostering an era of unprecedented industrial growth.
Transition to Steam Power
The change to steam power marked a pivotal shift in textile production, freeing mills from the limitations of water sources and enabling unprecedented operational consistency and productivity. During the Industrial Revolution, steam engines began to replace traditional water power in textile mills, allowing for continuous operation regardless of weather conditions or geographic limitations.
By adopting steam power, textile mills could significantly increase their efficiency. Steam engines provided a reliable and more versatile source of energy, capable of driving a variety of machinery within the mills. This not only boosted productivity but also allowed for the expansion of textile manufacturing into areas that previously lacked suitable water resources.
The evolution to steam-powered mills revolutionized the textile industry. You could now set up a mill in urban areas, closer to labor markets and transportation hubs, without relying on natural water sources. This change meant that textile production was no longer geographically constrained, leading to the proliferation of mills and a significant increase in output.
With steam engines, energy became a much more manageable and dependable commodity, driving the textile industry forward and laying the groundwork for modern industrial manufacturing.
Impact on Production
One can't overlook how the integration of steam engines into textile mills fundamentally reshaped production processes, driving unparalleled increases in efficiency and output. The advent of steam engines allowed textile mills to transcend the limitations of manual labor and water-powered spinning wheels. This technological leap optimized the use of groundbreaking inventions like the spinning jenny, amplifying their impact on production.
Steam engines facilitated continuous operation, drastically reducing downtime and enabling mills to maintain a relentless pace. As a result, the textile industry experienced a dramatic surge in production capacity, transforming it into a cornerstone of the Industrial Revolution. The newfound ability to operate on a larger scale meant that mills could produce textiles in quantities previously unimaginable, meeting the burgeoning demands of a rapidly growing market.
Consider the profound changes brought about by this innovation:
- Unprecedented efficiency: Steam-powered mills operated around the clock, maximizing output.
- Economic growth: The increased production capacity fueled the expansion of the textile industry, driving economic prosperity.
- Job creation: The boom in textile production created numerous employment opportunities, reshaping communities.
In essence, the integration of steam engines in textile mills didn't just revolutionize manufacturing processes; it wove the fabric of a new, industrialized world.
Impact on Global Economy
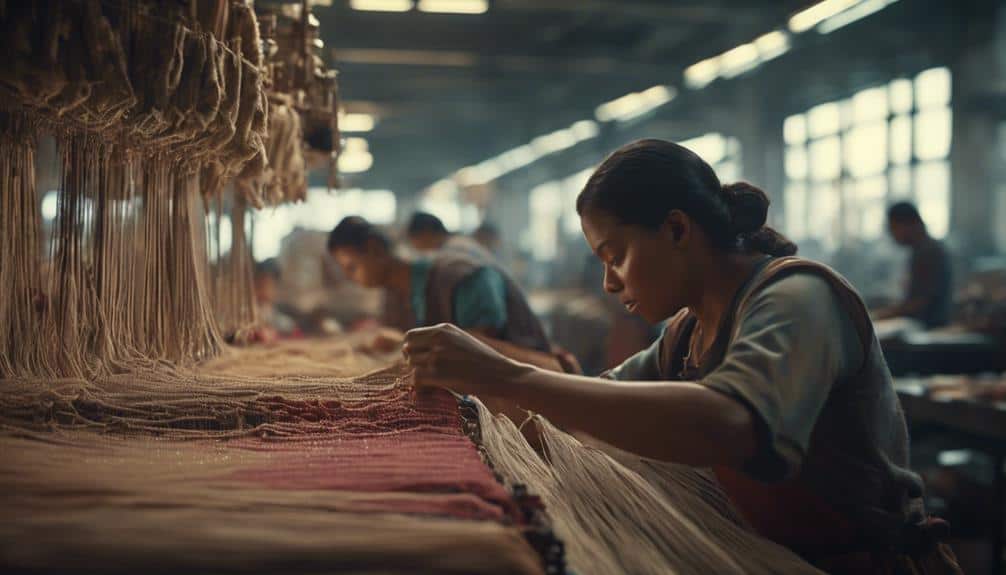
Innovations in the textile industry during the Industrial Revolution fundamentally transformed the global economy by markedly lowering production costs and boosting international trade. The introduction of the spinning jenny and the water frame revolutionized the textile industry, driving efficiency to unprecedented levels. These innovations facilitated mass production, making textiles, especially cotton, more affordable and accessible worldwide.
With lower cloth prices, demand for raw materials like cotton surged, stimulating global trade networks. These technological advancements not only reshaped the textile industry but also made cotton farming notably more profitable and efficient. As a result, regions specializing in cotton production, such as the American South, saw immense economic growth.
The modern factory system, born out of these innovations, centralized production and created new job opportunities, further integrating economies. This shift contributed to the rise of industrial capitalism, where nations with advanced textile industries gained economic power and influence on the global stage.
You can see how the ripple effects of these advancements extended beyond textiles, influencing transportation, finance, and global trade practices. The textile boom, driven by these key innovations, didn't just change how fabrics were made; it wove a new economic fabric for the world.